Team Russia VO70 Design (Seahorse – July 2008)
— 09 Jun 2008
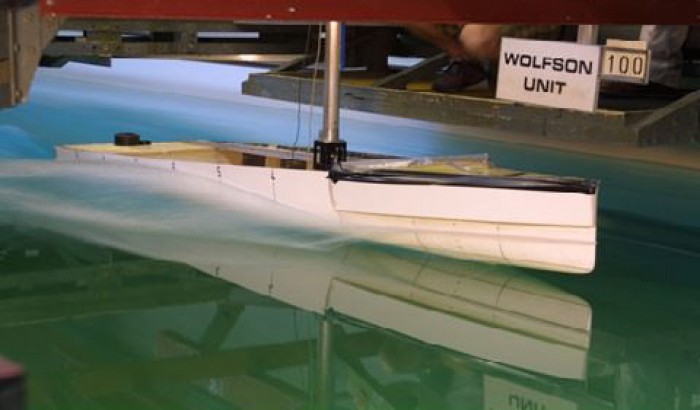
Stepped hull - speed 30 + water ballast
For any designer who is in the performance game it is almost impossible, when asked, to turn down the opportunity to design a boat for one of the round-the-world race formats, particularly the Volvo Ocean Race. With the 70s this race is still sufficiently embryonic as to pose some big questions, making the technical and creative challenge absolutely compelling. And by way of dividend one can look forward to an invariable trickle-back of knowledge that can filter its way into other spheres of one’s interest.
Thus it was with the Russian Challenge – a moment’s hesitation (these boundary-pushing projects are not for the faint-hearted – we know this from experience); then a headlong rush, not to say an adrenaline rush. ‘Awesome’ is not a word I generally use, but for these boats nothing seems to be a better fit. If one thinks in general sailing terms these boats are in a totally different part of the landscape. They are into a brave new world of performance and to think of them in conventional terms is immediately inhibiting if not a little naive. They are boats with an identity crisis; sticky and a little slow in the very light, but powerboats by any other name in a breeze.
They have an exceptionally low displacement:length ratio and a phenomenal power:weight ratio; fully canted the keel represents the equivalent to between 60 and 70 crew on the weather rail (without actually carrying that weight of crew). Even without the last race to look back on it is immediately obvious that these boats hunger for power. But with much of the Southern Ocean distance stripped away by the new course, would the imperatives remain the same for their second showing?
The starting point for this sort of project is the weather model, and for this we turned to Jure Jerman of the Slovenian Met Office who was helping us with our Class 40 Atlantic model. The general perception on the street was that the new course would be on the whole lighter, with a higher upwind component. But how light, how biased? These are key questions that need good answers, but the answers do not just fall out of a database. It takes time and a great deal of work; so too does the groundwork to the main design thrust. In our case we obviously had some benefit of experience – other designers’ experience. Juan K had done a great job with his ABN Amro boats, and most unusually the Farr office seemed to have been aiming their dart at a slightly displaced bull’s eye – unsuccessful as it turned out but elucidating nevertheless. These two schools of thought sat there as some sort of text book in the making; but still, one got the impression, the sheet of paper remained surprisingly clean with many questions left unanswered. So we embarked on our own systematic groundwork, running a parametric series of models through the tank as our first major task, in the process helping to set up the terrain for our VPP.
Tom will write about the process; I will skip here to the outcome of all this – a somewhat unusual looking boat that wove its way through extensive analytical testing to its final form. A creative approach is one thing; at this level a boat’s rationale has to withstand the rigours of scientific analysis. But, that said, even the most meticulous testing has also to withstand the scrutiny of logic. Legion are the occasions when blind faith in the numbers has led one astray, and for the older reader one only has to say ‘Mariner’ and all will be clear.
So, first the rationale. It is well understood that a high power:weight ratio solution in a sailing boat is likely to generate a disproportionate amount of wetted surface area, exposing it in light airs. But with masthead Code Zeros allowed for the next race, it became evident that these boats are going to be fully powered up in about 6-8 knots of breeze. So while there may be a lot of light air on the new course, it’s not light air as we know it. And it’s not just that this slow-speed regime has become a narrower band – out in the ocean, at least, one’s ability to impact on the light air potential of a boat is compromised by a disproportionate balance of luck. The boats are not going to be sailing alongside each other and the vagary of local wind variation is often a bigger filter of success than light air prowess per se.
Of course one does not comfortably give away light air performance willy-nilly; it’s just that if it’s a case of slant or bias, then it is abundantly clear in the context of this race and these boats that a light air-optimised solution is going to lose out significantly more in a breeze than will the power solution caught outside its preferred domain. The performance potential of these boats is such as to convince one that there must be work to be done at the top end – with substantial rewards to be reaped.
The most visible distinction between Team Russia and her known (as this was written) counterparts are the sprayrails – after all, they are not exactly subtle. But these are not add-ons as one might imagine but an integral part not only of the hull but of the entire concept, making it possible to entertain other features and characteristics that might not otherwise work. Indeed the boat is really a stepped hull rather than an accoutred hull. Yes, the steps should do a great job for spray but they do other things too. They generate lift; they add considerably to the reserve of buoyancy forward, and they allow one to contemplate a finer entry at lower topside level than one might without the benefit of that incremental reserve. And because the propensity to bow-bury will be somewhat reduced it encourages one to consider a concept of increased form stability with the hull’s beam carried a long way aft and a lower turn-of-the-bilge to the afterbody.
To anyone who has looked at photographs or video clips of the first generation boats at speed the benefit of some sort of spray control will be immediately obvious. At one level it will be much easier on the crew, an advantage that can translate itself into reduced fatigue potential and possibly a preparedness to drive the boat harder at the top end. At another level a reduction in spray and sheet water means parallel reduction in viscous drag and in displacement (a centimetre-depth of water on the deck is equal to little short of a tonne). Both are speed-sapping features and do little for crew efficiency or control.
Perhaps the biggest gain, however, is in lift at speed and in this respect we were seeing significant reduction in resistance with the bow wave driven back into the trough of its own creation.
Why two, not one or three, one may ask. The Volvo 70 rule has nothing to say about sprayrails or steps as such, but it does very comprehensively control what one can and cannot do about hollows, tumblehome, etc. In this respect there is some freedom forward, up to 7 metres abaft the stem where our steps stop suddenly, but the configuration one is able to weave through the nuances of the Rule’s intricate text is potentially a little prescriptive. Thus our upper step cannot be bigger in volume than that defined by the sheer in plan and by the height of the base of the step – in our case an extension of the chine. In itself it creates a massive increment in buoyancy reserve, but alone would create a shocking re-entry in a seaway. The lower step, generated out of the upper one, eases the re-entry transition and creates a lifting edge at speed, closer to the dynamic waterplane. A third step was contemplated but dismissed for reasons of weight effectiveness.
What was particularly interesting in the wave tank was the behaviour of the model with respect to pitching. While one obviously cannot generate oblique seas in a wave tank, clues given even by a direct headsea are invaluable in a generalised way. It was evident that not only was the motion or pitch amplitude of the stepped hull significantly less than the control hull, with the actual bow-burying much less, but that the general re-entry was relatively soft, with a more exponential than stepped pick up of buoyancy.
All of this is the upside. The downside is the potential propensity of the lower step to drag in the light-to-moderate with heel, and a possible compromise would have been a reduced length lower rail, more closely conforming to the heeled waterline of the boat. However, it’s all about strategy – the choice between building on a strength versus damage limitation, and given the substantial powerboat design work we have carried out of late we can see gains at the top end that no end of slow-speed finesse will outweigh. Retractable steps would of course be interesting, but that’s one that can’t find its way through the rule net.
What else comes out of the steps? Given that flying spray will be somewhat diminished we did not feel compelled to adhere to the razor-sharp entry that some high speed sailing boats are constrained to in the hope and prayer that water will stay where it belongs. The Volvo 70 rule is a restricted rule; with a maximum overall length provision, the quality of this length is a major speed determinant and in our view that piece of length which is dedicated to defining a sharp cutwater would really be better employed in the middle of the boat where it can have major impact on the hull’s volumetric distribution, allowing a more appropriate prismatic coefficient. This was backed up by evidence we gained from the tank, and although it’s not a pretty bow it seems to pay for its way just as it has done in the IACC arena.
Of course it wasn’t a case of cutting a piece from here and adding it there, but by way of explaining the rationale it’s a useful metaphor. And the other related subject is that with the boat’s longitudinal asymmetry, possibly more delta-shaped than some of the other boats, it trims with heel to an off-axis plane such that a sharp entry would be more prone to trip the flow over the forebody.
This leads very nicely to another piece in the jig-saw puzzle. With our wide beam carried all the way aft, and with low, powerful chines to boot, the upright wetted area can be nothing but high. But just as a performance dinghy can have heel induced, these boats have 40 degrees’ worth of keel cant angle adjustment to do just that, and with such a hull form the wetted area plummets with heel at a much faster rate than a hull which has been compromised to achieve a moderately low upright wetted area. Indeed, the boat as designed has two effectively independent hull forms. The heeled hull is of very narrow waterplane with a relatively straight axis, and in line with this the daggerboard location has been driven by a quest to keep it away from the free surface as much as is possible, throughout the range of operational heel angles. Version 2 of the Rule does not allow games to be played with the main keel pin orientation and with a forward trimming moment with heel the fin will produce negative lift upwind, i.e. dynamic righting moment. In our case the trimming moment will be slightly greater than most of the others and the righting moment bonus proportionately greater.
Of course some of the characteristics we have built into Team Russia come at a cost in weight, in a class which somewhat unhealthily rewards an osmotic migration of grammes from virtually everywhere in the boat to the keel and ultimately the bulb. This is unquestionably a key feature of performance, but experience tells one that obsessive pursuit of this target does not in itself lead to podium guarantee. Apart from the obvious ‘to win one has to finish’, it doesn’t necessarily bear out on the track, as the guys on Ericsson seemed to discover last time round, with reputedly the heaviest bulb.
There is much else that one could say but this probably covers the most distinctive aspects of the boat. With none but serious efforts in this race there will be other points of view and other perspectives that may in the event carry more sway. Nevertheless, for us it has been a fascinating project, and a privilege to be on the park at a time when the playing field itself is still a little uneven. It makes it more interesting and it means that cash is not necessarily king. It seems no secret that some other campaigns have enjoyed a much larger budget, but what I can say is that I believe we would be in the same philosophic corner of the design space had we had an even more substantial testing budget. That the Russian Challenge is a little unusual has nothing to do with difference for difference’s sake. It’s simply an assimilation of what we can see from the past set against the opportunities of the future.
Tom Humphreys:
Our design process kicked off with an in depth analysis of the previous edition of the Volvo Ocean Race. Design interpretations of the V1 boats were modelled as accurately as possible so we could start to get a handle on the performance crossovers that existed between the Farr and Juan K designs. A systematic series of beam variants were run in the towing tank to investigate the trade-offs between form stability and wetted surface area. Our base boat at this stage was the mid beam model which was our interpretation of ABN 1. It was felt important to include this in our testing as it formed a link to what was known from the last race and acted as a very useful control. During this time Jure Jerman was working on a weather model for the race which, along with the tank test data, formed the terrain for our VPP. With this set, a multitude of hull forms were then run through the VPP to identify any sweet spots in terms of stability against wetted surface area that might exist on each leg. The VPP work and initial weather routing carried out by Jure also enabled us to put some statistics to the likely boat speeds, wind speeds and angles, sail usage, etc, so we could start to focus in on the high percentage areas (though with the race course yet to be finalised at this stage it was all kept fairly broad brush). With a picture now developing as to the general hull shape characteristics we felt desirable, our next stage in the process involved re-visiting the towing tank to look at some finer resolution design details, including appendage geometries, bow bluffness and spray rails.
With the HYD office coming fresh off the back of a high speed (56 knots with hopefully more to come!) 37 metre motor yacht project it is clear for everyone to see that a bit of power boat thinking has found its way into our VO70 design! Looking at footage from the last race we always felt these boats were crying out for spray rails to reduce the amount of added mass of the spray on deck and spray wetting (once the forward topsides start immersing there is often a tendency for the bow to get sucked deeper into the water, and in tandem there is an added frictional drag component). In order to test this we visited the high speed GKN towing tank in Cowes, re-running one of our earlier beam series models before retrofitting steps to it and running it again down the tank. Even at a first glance we liked the look of them with everything seeming to be that much cleaner and once the results were processed we were seeing significant and increasing upright drag reductions from about 14 knots boat speed. The stepped hull high speed runs also resulted in a significantly more bow up trim due to dynamic lift generated by the rails, which has encouraged a fairly straight run aft on our final design to promote early planing. When my father designed the hull for the Open 60 Kingfisher some increased rocker was developed into the afterbody to discourage bow burying, at some cost to speed; with the steps we have felt less constrained in this respect.
The control and stepped hulls were also run into waves to check for any adverse effects. While waves will rarely be encountered head on by sailing boats it was felt that it could provide a useful insight into how these boats would behave upwind in a seaway and how the reserve buoyancy of the hull steps could influence pitch motion (particularly with leg 4 from Singapore to Qingdao in mind which is likely to be a heavy air upwind slog with wind against current). The control and stepped hull models were run at typical upwind speeds and heel angles and what was most interesting was the reduction in pitch motion recorded. While there was not much difference to the height of the peak of this motion as each new wave was encountered, the bottom of this motion was significantly shallower on the stepped hull due to the reserve buoyancy of the steps being picked up on re-entry, cutting down the full extent of this energy sapping motion.
Another area investigated was the bluff bow which we have long been considering for designs governed by a length restriction and my father has always had a notion that you could delude a boat into behaving above its actual length. This is obviously nothing new and it looks to have been the thinking behind a number of the bluff bowed version 5 IACC designs. In order to test this, one of the earlier beam series models was again modified from amidships forward to incorporate the bluff bow and now extended midbody. Runs were done both upright and heeled and compared to the control model. Again some significant drag reductions were recorded above 10.5 knots boat speed both upright and at various heel angles.
This outlines some of the testing procedures used to arrive at our more noticeable design features. As we see it, our design is really based on two levels of thinking. Firstly there was the juggling act between form stability and wetted surface area, of which maximum beam, waterline beam, chine height, etc all played a part. The second level included the more detailed design features of which the hull steps have had the most significant impact on our design concept. Without the hull steps it probably wouldn’t be possible to push the stem bluffness as much as we have as it can generate a lot more spray. However testing really demonstrated how effective the steps could be at shedding spray and reducing bow burying and it is their inclusion that encouraged us to incorporate the bluff bow along with a pretty fine half angle of entry and very straight rocker profile and flat aft sections. A model of our final hull lines incorporating all these features was built and run in the towing tank before Green Marine commenced on the tooling to double check our design choices and to start looking at different appendage geometries. We also spent time at the Twisted Flow Wind Tunnel in Auckland which along with the tank data enabled us to update the aero and hydro models in the VPP to provide us with accurate polars for the boat (extremely important for the weather routing and its knock-on effects on sail usage / design, etc, as well as logistics planning by the team).
Photo: Wolfson Unit